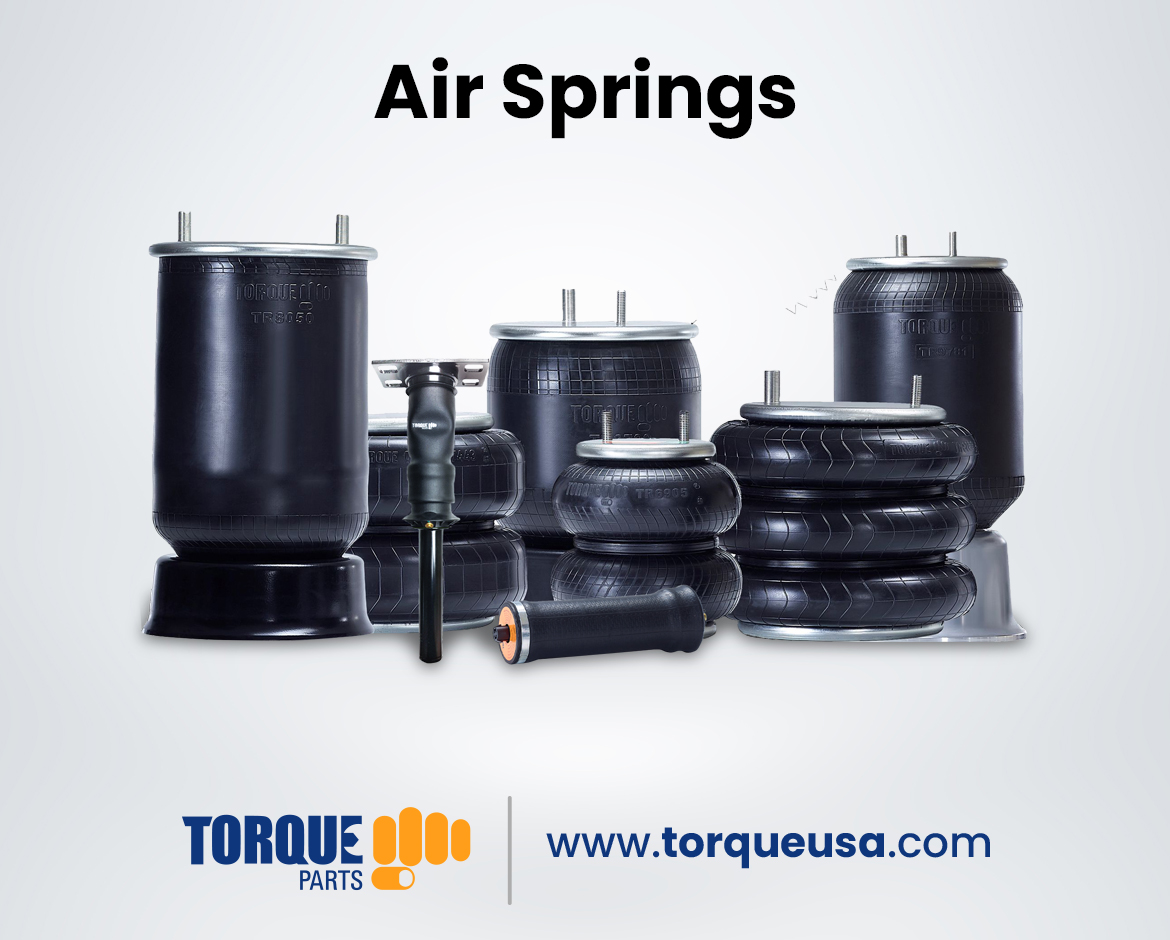
Air Springs Types, Components, Applications, Benefits, Maintenance, and Selection Guide
Introduction to Air Springs
Air springs are a type of suspension system that uses compressed air to support and cushion heavy loads. They are commonly used in a wide range of applications, from heavy-duty vehicles and industrial machinery to passenger cars and aircraft.
Unlike traditional steel springs, which rely on mechanical resistance to absorb shocks and vibrations, air springs use the compressibility of air to provide a smoother and more comfortable ride. When the load is applied to the air spring, the air inside is compressed, which in turn increases the spring rate and provides greater resistance.
Air springs have several advantages over traditional springs, including a more consistent performance, greater load-carrying capacity, and the ability to adjust the spring rate and ride height on the fly. They are also more durable and require less maintenance than traditional steel springs.
In this article, we will explore the different types of air springs, their components, applications, benefits, maintenance requirements, and selection criteria. Whether you are an engineer, a mechanic, or a vehicle owner, this guide will help you understand the key aspects of air springs and how to choose the right one for your needs.
Types of Air Springs
There are several types of air springs available in the market, each with its own unique design and applications. The most common types of air springs are convoluted air springs, rolling lobe air springs, sleeve air springs, bellows air springs, and piston air springs.
For some types of air springs:
Air Springs
Convoluted air springs, also known as single-convoluted or double-convoluted air springs, are the simplest and most common type of air spring. They are made of a single or double layer of rubber with a convoluted shape that provides the spring force. They are commonly used in heavy-duty trucks and trailers, as well as in industrial and off-road equipment.
Rolling lobe air springs, also known as rolling sleeve air springs, are similar to convoluted air springs but have a rolling lobe design that provides a more linear spring rate and smoother ride. They are commonly used in passenger cars, luxury SUVs, and light trucks.
Sleeve air springs, also known as sleeve-type air springs, are made of a rubber sleeve that encloses a metal piston. They are commonly used in industrial machinery and off-road equipment, as they can provide a large amount of spring travel and weight-carrying capacity.
Bellows air springs, also known as convoluted bellows air springs, are made of multiple layers of rubber with a bellows-shaped design that provides a high spring rate and greater stability. They are commonly used in rail cars and heavy-duty off-road equipment.
Piston air springs, also known as air-over-piston air springs, are made of a metal piston that moves inside a cylinder filled with compressed air. They are commonly used in heavy-duty trucks and trailers, as they can provide a high spring rate and precise control of the ride height.
By understanding the differences between the types of air springs, you can choose the one that best fits your specific application and requirements.
Components of Air Springs
Air springs consist of several key components that work together to provide a smooth and reliable suspension system. These components include the air spring body, end caps, piston, mounting hardware, connection points, and valve systems.
The air spring body is the main component of the air spring, and it is made of several layers of rubber or synthetic material that can withstand the pressure of compressed air. The body also has a specific shape and design that provides the necessary spring force and travel for the application.
End caps are located at both ends of the air spring body and provide a secure connection point for the mounting hardware. They also contain the piston and valve systems that regulate the air pressure inside the air spring.
The piston is a metal or plastic component that moves inside the air spring body and compresses or expands the air volume to adjust the spring rate and ride height. It is typically connected to the vehicle frame or suspension system through mounting hardware.
Mounting hardware is used to secure the air spring to the vehicle chassis or suspension system. It can include brackets, bolts, nuts, and washers that provide a secure and stable connection between the air spring and the vehicle.
Connection points are the ports or fittings located on the end caps that allow the air spring to be connected to an air supply system. They are typically threaded or push-to-connect fittings that are compatible with various types of air lines and valves.
Valve systems are the components that regulate the air pressure inside the air spring and allow for adjustments to the spring rate and ride height. They can include manual or automatic valves, pressure sensors, and control modules that work together to provide a reliable and efficient suspension system.
By understanding the different components of air springs, you can better diagnose and troubleshoot any issues with the suspension system and ensure that the air springs are properly installed and maintained.
Applications of Air Springs
Air springs are widely used in various industries and applications, because of their superior performance, durability, and versatility. Some of the most common applications of air springs are heavy-duty vehicles, industrial machinery, off-road equipment, passenger cars, rail cars, and aerospace.
Heavy-duty vehicles, such as trucks, buses, and trailers, use air springs to supply a smooth and stable ride, even under heavy loads. Air springs can also improve the safety and handling of these vehicles by reducing vibration and improving stability.
Industrial machinery, such as compressors, generators, and pumps, use air springs to isolate and dampen vibration and noise. This helps to improve the lifespan and reliability of the equipment and reduce maintenance costs.
Off-road equipment, such as excavators, loaders, and bulldozers, use air springs to provide a stable and durable suspension system that can withstand harsh working conditions. Air springs can also improve the comfort and safety of the operator by reducing the impact of shocks and vibrations.
Passenger cars, especially luxury cars and SUVs, use air springs to provide a smooth and comfortable ride, as well as to enhance the handling and stability of the vehicle. Air springs can also improve fuel efficiency by reducing drag and improving aerodynamics.
Rail cars, such as freight cars and passenger cars, use air springs to offer a reliable and efficient suspension system that can handle various loads and speeds. Air springs can also reduce the impact of shocks and vibrations on the cargo or passengers and improve the safety and stability of the train.
Aerospace, such as commercial and military aircraft, use air springs to provide a lightweight and efficient suspension system that can withstand extreme temperatures and pressures. Air springs can also improve the comfort and safety of the passengers and reduce the maintenance costs of the aircraft.
By understanding the various applications of air springs, you can better appreciate their versatility and importance in modern industries and transportation.
Benefits of Using Air Springs
Air springs offer several benefits over traditional steel springs and other suspension systems. Some of the key benefits of using air springs include improved ride comfort, reduced vibration and noise, increased stability and control, enhanced durability and lifespan, lower maintenance costs, and eco-friendliness.
Improved ride comfort: Air springs can provide a smoother and more comfortable ride than traditional steel springs, thanks to their ability to absorb shocks and vibrations more effectively. This can reduce driver and passenger fatigue and improve the overall driving experience.
Reduced vibration and noise: Air springs can isolate and dampen vibration and noise more effectively than traditional steel springs, thanks to their design and materials. This can improve the durability and lifespan of the vehicle or equipment and reduce the risk of damage or wear.
Increased stability and control: Air springs can supply greater stability and control over the vehicle or equipment, thanks to their ability to adjust the spring rate and ride height on the ride. This can improve the safety and handling of the vehicle or equipment, especially under heavy loads or rough terrain.
Enhanced durability and lifespan: Air springs are more durable and longer-lasting than traditional steel springs, due to their materials and design. They are less prone to fatigue, corrosion, and wear, and can withstand harsh environments and heavy loads.
Lower maintenance costs: Air springs require less maintenance and replacement than traditional steel springs, thanks to their durability and reliability. They also require fewer components and lubrication, which can reduce the overall maintenance costs and downtime.
Eco-friendliness: Air springs are more eco-friendly than traditional steel springs, thanks to their lightweight and recyclable materials. They can also improve fuel efficiency and reduce emissions by reducing drag and improving aerodynamics.
By understanding the benefits of using air springs, you can better appreciate their value and importance in modern industries and transportation.
Maintenance and Repair of Air Springs
Air springs are designed to be durable and low-maintenance, but they still require regular inspection and upkeep to ensure optimal performance and lifespan. In this chapter, we will discuss the maintenance and repair of air springs, including inspection and testing, replacement and installation, common problems and solutions, and tips for prolonging air spring life.
Inspection and testing: Air springs should be inspected regularly for signs of wear, damage, or leaks. This can involve visual inspection, pressure testing, and load testing to ensure that the air spring is performing as intended. Any issues or abnormalities should be addressed immediately to prevent further damage or failure.
Replacement and installation: When an air spring needs to be replaced, it is important to choose the right replacement part and follow the manufacturer’s installation instructions carefully. This can involve removing the old air spring, cleaning the mounting surface, and installing the new air spring with the correct torque and alignment.
Common problems and solutions: Some common problems with air springs include leaks, cracks, punctures, and wear. These issues can be caused by various factors, such as age, usage, and environmental conditions. Solutions can include patching or replacing the air spring, or addressing the underlying cause of the problem.
Tips for prolonging air spring life: To prolong the lifespan and performance of air springs, it is important to follow the manufacturer’s recommendations for maintenance, usage, and storage. This can include regular cleaning, proper inflation, and avoiding overloading or harsh impacts. It is also important to address any issues or abnormalities as soon as they arise.
By understanding the maintenance and repair of air springs, you can ensure that your suspension system is operating at peak performance and reliability. Regular inspection, testing, and upkeep can help prevent costly repairs and downtime, and ensure a smooth and comfortable ride.
Choosing the Right Air Spring
Choosing the right air spring for your application is critical to ensuring optimal performance and reliability. In this chapter, we will discuss the factors to consider when choosing an air spring, including the application, load capacity, spring rate, mounting options, and compatibility with other components.
Considerations for selecting the right air spring: When selecting an air spring, it is important to consider the specific application and usage requirements, such as the vehicle type, load capacity, and operating environment. Other factors to consider can include the desired ride height, stiffness, and damping characteristics.
Matching the air spring to the application: Each type of air spring is designed for specific applications and load capacities. It is important to choose the air spring that is compatible with your application and meets your requirements for performance, durability, and reliability.
Consulting with air spring manufacturers and suppliers: Air spring manufacturers and suppliers can provide valuable guidance and expertise in selecting the right air spring for your application. They can also provide technical specifications and performance data to help you make an informed decision.
Factors affecting air spring performance: Several factors can affect the performance and lifespan of air springs, including overloading, underinflation, misalignment, and environmental factors such as temperature and humidity. It is important to address these factors to ensure optimal performance and reliability.
By understanding the factors to consider when choosing an air spring, you can ensure that your suspension system is properly matched to your specific application and usage requirements. This can improve the safety, comfort, and reliability of your vehicle or equipment, and help prevent costly repairs and downtime.
Conclusion: The Benefits and Versatility of Air Springs
Air springs are a versatile and reliable suspension system that offer several benefits over traditional steel springs and other suspension systems. They are widely used in various industries and applications, from heavy-duty trucks and industrial machinery to passenger cars and aircraft.
By using air springs, you can improve ride comfort, reduce vibration and noise, increase stability and control, enhance durability and lifespan, lower maintenance costs, and contribute to a more eco-friendly transportation system. With the right selection, installation, and maintenance, air springs can provide a reliable and efficient suspension system that can withstand harsh working conditions and heavy loads.
In this article, we have explored the different types of air springs, their components, applications, benefits, maintenance requirements, and selection criteria. By understanding these key aspects of air springs, you can make informed decisions and optimize the performance and reliability of your suspension system.
Whether you are an engineer, a mechanic, or a vehicle owner, air springs are an important and valuable component of modern transportation and industry. By choosing the right air spring for your application and following best practices for installation and maintenance, you can ensure a smooth and comfortable ride, reduce downtime and repair costs, and contribute to a more sustainable and efficient transportation system.
For detailed information, you can contact us at
torqueusa.com.